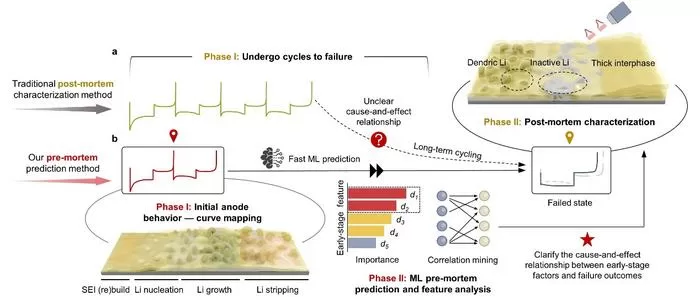
Lithium metal batteries (LMBs) are a promising technology for next-generation energy storage, offering higher energy density than traditional lithium-ion batteries.
However, challenges related to the anode’s behavior—specifically issues related to its kinetics and reversibility—have hindered their widespread adoption. Researchers have long struggled with understanding the underlying causes of battery failure, often relying on post-mortem analysis that only reveals outcomes but fails to capture the dynamic processes leading to failure.
In a groundbreaking study, researchers at Tsinghua Shenzhen International Graduate School and the Shenzhen Institute of Advanced Technology, Chinese Academy of Sciences, have developed a predictive model that uses electrochemical data from the initial cycles of LMBs to forecast potential failures.
This model identifies early indicators that correlate with different types of anode failure. The research demonstrates that failure signatures in the initial cycles serve as “electrochemical fingerprints,”—providing key insights into the failure mechanisms of lithium metal anodes.
“We discovered that early-stage lithium plating and stripping behaviors during the first two cycles are highly indicative of the battery’s eventual failure mode,” said first author Zhihong Piao. “This breakthrough model not only predicts the failure type accurately but also reduces the time and resources needed for testing.”
By leveraging machine learning algorithms and extensive datasets, the team developed a high-accuracy classification model that distinguishes between three main failure types: kinetics degradation failure, reversibility degradation failure, and co-degradation failure.
It also demonstrates generalizability, accurately classifying failures in cells using a wide range of published electrolyte formulations—including low- and high-concentration systems based on carbonates, ethers, and siloxanes.
Instead of waiting weeks or even months for a battery to degrade, engineers and researchers can now forecast its future in a matter of days. This offers a major advantage in both speed and cost, especially when developing and testing new electrolyte formulas or battery designs.
What makes this approach even more powerful is that it doesn’t require any disassembly or special instruments—it works using cycling data that the battery produces. This makes it highly practical and easy to adopt in both academic labs and commercial production lines. This opens up new possibilities for designing more robust batteries, optimizing electrolytes, and accelerating the development of LMB technologies.
Notably, the research offers more than just a predictive tool—it provides scientific insights into failure mechanisms. The research reveals the importance of the solid electrolyte interphase (SEI) and the lithium deposit microstructure in determining battery performance.
The team validated this with experiments and simulations, linking observed electrochemical behaviors to specific SEI properties and lithium morphology. These two features influence the formation of ineffective interphase regions (lacking intimate contact with the lithium metal) and inactive lithium at the lithium metal anode, which in turn lengthens charge carrier (lithium-ion and electron) transport paths, leading to poorer kinetics and reversibility.
The work was supported by multiple national and provincial research programs of China. The research team believes this method can not only accelerate battery development but also provide a foundation for a deeper understanding of lithium metal battery behavior under real-world conditions.