Integration of a Hime Diamond into the Device Simplifies Measurement of Electrical Resistance under Ultra-High Pressure.
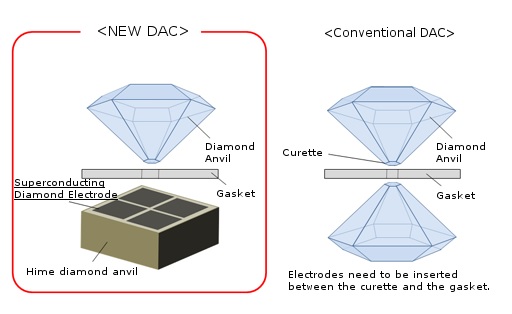
Source : NIMS
Researchers of National Institute of Materials Science and Ehime University, Japan, developed a new diamond anvil cell by micro-fabricating a superconducting diamond, which conducts electricity like metal and serves as electrodes, on the world’s hardest and chip-proof nano-polycrystalline diamond.
A research group led by Yoshihiko Takano, a leader of the Nano Frontier Superconducting Materials Group, Environment and Energy Materials Division, NIMS, and another research group led by Tetsuo Irifune, a director of the Geodynamics Research Center (GRC), Ehime University, jointly developed a new diamond anvil cell (DAC) by micro-fabricating a superconducting diamond, which conducts electricity like metal and serves as electrodes, on the world’s hardest and chip-proof nano-polycrystalline diamond (Hime diamond). As a result, the conventional practice of skillfully attaching four electrodes to a small sample (of several dozen microns) was eliminated, and thus electrical resistance measurements under ultra-high pressure have become much easier. Furthermore, because diamond electrodes can be used repeatedly, physical property measurements have dramatically improved in terms of work and economic efficiencies.
[pullquote]Accordingly, research group micro-fabricated superconducting diamond electrodes on the top of the anvil using the electron-beam lithography method.[/pullquote]
As shown in the right diagram in Figure , a typical DAC is a device to generate high pressure by pressing curettes of paired diamond anvils on each other. To increase the pressure generated by the device, it is necessary to make the areas of the curettes smaller. Specifically, to generate ultra-high pressure (several hundreds of thousands of atmospheric pressure), curettes need to be about 400 microns in diameter.
Operation of such a device would be very difficult due to the requirement that the sizes of the samples to be studied need to be as small as about 100 microns. To generate a million atmospheric pressure or higher, the sizes of the samples need to be even smaller, making it extremely challenging to manually attach electrodes to the samples.
Accordingly, research group micro-fabricated superconducting diamond electrodes on the top of the anvil using the electron-beam lithography method. As it is convenient to use a plate-shaped diamond for the fabrication of electrodes using lithography, they combined a plate-shaped diamond and another diamond with a curette to form a diamond anvil cell with its shape as shown in the left diagram in Figure .
As a result, research group succeeded in developing a new diamond anvil cell by combining the world’s hardest diamond electrodes and the world’s hardest diamond anvil. Because advanced experimental technologies are required, materials R&D under ultra-high pressure is still largely unexplored. As such, this field has great potential to offer opportunities for exploring novel materials and superconductors with extraordinary functions. We believe that this new technology will contribute to Japan’s advancement in materials development.
A part of this research was supported by the Premier Research Institute for Ultrahigh-pressure Sciences (PRIUS), which has been recognized by the Ministry of Education, Culture, Sports, Science and Technology as a shared-use research facility.
This study was presented on February 23 at a PRIUS Symposium to be held at the Geodynamics Research Center (GRC), Ehime University.